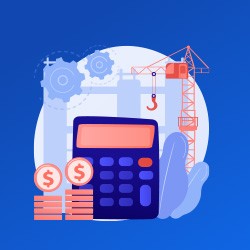
Production Costing System:
- Full integration with Al Motakamel of Inventory Control System and Production Control System.
- Full integration with Al Motakamel of General Ledger System.
- A complete description of all production and service centers inside the factory in terms of the maximum operating hours for each center, the cost elements associated with it, and the estimated cost for each element within the center.
- The possibility of defining main and subsidiary cost elements.
- The possibility of determining the standard cost of cost centers.
- The possibility of determining the loading rates of the cost of the service centers over the production centers.
- The possibility of calculating the estimated cost of any product before issuing works orders for it (product assay).
- The possibility of calculating the cost of the product based on the actual expenses in General Ledger and the actual cost of the issued materials, and the actual operating hours or on based on the estimated expenses and the standard operating hours (according to the choice when evaluating the product).
- The possibility of analyzing the cost of any product at the level of its cost elements.
- Comparing the estimated cost of any product with its actual cost in terms of the following:
- Issued raw materials deviations (quantity/value).
- Operating hours deviations (numbers/value).
- Expenses deviations.
- Comparing the estimated cost of any product with its actual cost at the level of:
- Work orders.
- The products that were produced.
- Production and service cost centers.
- The possibility of producing more than one product in the same work order with the possibility of allocation cost to these products using a loading rates feature.
- Linking the cost of the issued and returned raw materials from stores with the Production Costing System.
- The possibility of evaluating the finished product vouchers received from production in stores without any posting in the Inventory Control System.
- Generating cost lists for the finished products and the semi-finished products.
Some of the Production Costing System Reports:
- Report on the comparative cost of the work order.
- Report on the cost list for the finished products.
- Report on the cost list of each production center and service center.
- Report on the balances of the production area on a specific date (Work in Process balances).
- Report on the cost analysis at the level of each stage of production.
- Report on the estimated budget of the cost centers.
- Report on the estimated budget of the cost elements.
- Report on the cost of what has been produced.
- Analysis of extraordinary expenses on work orders.
- Many other reports.