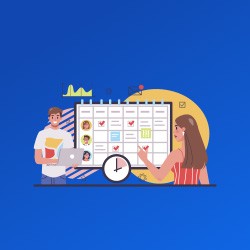
Production & Capacity Planning System:
Planning Production Orders based on Customer Orders or Sales Forecasts (Sales plans) from the marketing department.
- Arranging Production Orders according to a classification depends on priorities.
- Accurate definition of production resources (production lines - labor - tools) that includes working times, vacations, and periodic maintenance dates.
- Purchasing planning by issuing Purchase Requisitions to Purchasing Department to provide the needs necessary raw materials based on the available stock balances and the goods on the road.
- Reservation of raw materials in the stores.
- Allocation of the Production Orders between production resources.
- Possibility of applying JIT, JITO, or PLANNED policy in planning Production Orders.
- Generate Production Orders for each finished or semi-finished product in accordance with the applicable planning policy as shown in the previous point.
- Determine the starting and ending times for each generated Production Order for production.
- Allocation of loads between production sources.
- The possibility of trying more than one scenario for generating Production Orders and loading loads between production resources before the final approval.
- An Approval screen to define one scenario for generating Production Orders.
Bill of Materials (B.O.M):
- Bill of Materials including semi-finished and finished products.
- Possibility of registering more than one BOM for the same product.
- Dealing with normal deviations (compulsory) within the BOM.
- A special treatment to deal with the changing proportions of the active substance and its impact on the complementary materials in the BOM (such as the pharmaceutical industry).
- Allocation of components over the production stages of the product.
- Dealing with alternative items.
- Recording a validity date for the BOM.
Production Resources Planning:
- Dealing with all types of production resources (machines - labor - tools).
- Dealing with the measurement of production capacity in time or units.
- Dealing with more than one calendar for each production resource.
- Dealing with more than one shift per production resource.
- Definition of all production resources and their characteristics by the user.
- Dealing with operating through third-party systems.
Production Routes Planning:
- Dealing with more than one production route to produce a specific product.
- Linking each production route with several products.
- The possibility of dealing with production operations for each production line or production route.
- Handling the simultaneous operations, which have an overlap during the production process, whether the overlap is:
- By Time.
- Or by a percentage of the time.
- Or by Quantity.
- Dealing with fixed and variable time for each operation.
- Supports operating through third-party.
- Testing of the production route before executing it.
Items Planning:
- Designing a schedule and plan for the supply of each raw material based on the supplier.
- Designing a time plan based on a fixed and variable period for the supply of each raw material for each supplier.
- The possibility of dealing with more than one production route and more than one BOM for each finished product or semi-finished product depends on:
- Client.
- Client delivery place.
- Approve more than one policy for creating Production Orders:
- Batch.
- Production Order for each quantity.
- Lot for each Customer Order.
Creating Production Orders & Planning the schedule:
- Support the limited and unlimited planning methods.
- Plan production orders based on each of the based-on Customer Orders or Sales Forecast (Sales Plan).
- Several criteria for creating production orders such as:
- Create Production Orders based on customers.
- Create Production Orders based on Customer Orders or Production Plans.
- Create Production Orders based on the dates of Customer Orders or Production Plans.
- Create Production Orders based on priorities.
- Planning according to creating groups of raw materials stores and not only one store.
- Determining the start and end date of the Production Orders according to three methods:
- JIT.
- JITO.
- Planned.
- Multiple handling for the generated Production Orders:
- Not approving the Production Order.
- Consent & approval of the Production Order.
- Amending the date of the production Order.
- Graphs to follow up the loading percentage of the production resources.
- Issuing a report on the needs of raw materials and components.
- Reservation of raw materials in favor of the Production Order.
- Automatic creation of Purchase requisitions according to the needs of Production Orders, stock balances, and goods on the road.